- Mob/WhatsApp/Skype/Whchat: +86 18103817770
- E-mail: info@refractoryplant.com
Magnesia chrome bricks are made from sintered magnesia, fused magnesia, and fused magnesia-chrome as raw materials, through high pressure molding, drying and high temperature firing.
Main applications: Non-ferrous furnaces, cement kilns,glass furnaces, EAF, VOD, AOD, RH etc.
Magnesia chrome bricks are featured with less impurity content, high bulk density, good slag resistance, strong erosion resistance, high temperature volume stability, good thermal shock resistance. Magnesia chrome bricks refractoriness is more than 2000℃, its refractoriness under load is generally above 1550℃.
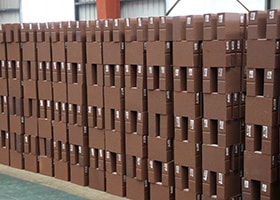
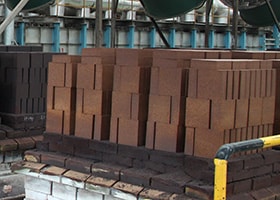
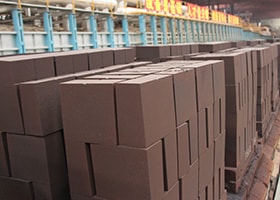
Application
- Cement industry: cement rotary kiln burning zone.
- Metallurgical industry: refining ladle permanent layer, electric furnace top, and other kinds of non-ferrous metal smelting furnace.
- Others: Lime kiln or other high temperature furnace linings.
Magnesia Chrome brick shapes can be customized according to drawings.
Magnesia Chrome bricks can be divided into Common Magnesia Chrome brick, Direct-Bonded Magnesia Chrome Brick, Semi-rebond Magnesia Chrome Brick, Rebonded Magnesia Chrome Brick, etc.
Direct-Bonded Magnesia Chrome Brick is made of pure raw materials and high firing temperature. The so-called direct combination refers to there is more direct contact between chrome ore particles and magnesia. There is less SiO2 in raw materials (controlled in 1%-25%), and silicate generation amount is little. The silicate is extruded into the corner of solid particles under high temperature firing.
Direct-Bonded Magnesia Chrome Brick has features of high strength, good slag resistance, good erosion resistance, scouring resistance, corrosion resistance, excellent thermal shock stability and good volume stability at 1800℃.
Rebonded Magnesia Chrome Brick is made by electrofusion method to melt magnesia-chrome mixture powder, then electrofusion magnesia chrome powder is crushed into certain particle sizes, then goes though high pressing machine, and is sintered by high temperature afterwards.
Rebonded Magnesia Chrome Brick has similar properties compared to the fused casting brick, but has better thermal shock resistance and better microstructure. Rebonded Magnesia Chrome Brick high temperature properties are between the fused casting brick and direct-Bonded Magnesia Chrome Brick .
Fused magnesia chrome brick is completely fused by placing the mixture of magnesia and chrome ore in an electric arc furnace, and then injecting the melt liquid into a refractory mold for casting. Fused magnesia chrome brick has excellent high temperature strength and slag corrosion resistance.
Fused magnesia chrome brick is same as fused magnesia-chrome material, with high density, good slag resistance, which has better slag resistance than direct-bonded magnesia chrome brick, but has weaker thermal shock resistance.
Tips:
- MGe6/MGe8/MGe12/MGe16=Commom Magnesia Chrome Brick
- DMGe6/DMGe8/DMGe12/DMGe16=Direct-Bonded Magnesia Chrome Brick
Model | MGe6 | MGe8 | MGe12 | MGe16 | DMGe4 | DMGe8 | DMGe12 | DMGe16 |
MgO % | 80 | 72 | 70 | 65 | 85 | 77 | 74 | 69 |
Cr2O3 % | 7 | 10 | 13 | 17 | 5.5 | 9.1 | 14 | 18 |
CaO % | 1.2 | 1.2 | 1.2 | 1.2 | 1.1 | 1.4 | 1.2 | 1.2 |
SiO2 % | 3.4 | 4 | 4 | 4.2 | 1.3 | 1.2 | 1.2 | 1.5 |
Al2O3 % | 4.5 | 6.5 | 6 | 6 | 3.5 | 4 | 3.5 | 4.5 |
Fe2O3 % | 4 | 4.8 | 5.5 | 6.5 | 3 | 6.4 | 5 | 5.7 |
Apparent Porosity % | 17 | 18 | 18 | 18 | 18 | 18 | 18 | 18 |
Bulk Density g/cm3 | 3 | 3 | 3.02 | 3.05 | 3.02 | 3.04 | 3.06 | 3.08 |
Cold Crushing Strength Mpa | 55 | 55 | 55 | 50 | 50 | 50 | 55 | 55 |
Refractoriness Under Load °C | 1600 | 1600 | 1600 | 1600 | 1700 | 1700 | 1700 | 1700 |
Thermal expansion % 1000°C | / | / | / | / | 1 | 1 | 1 | 0.9 |
Thermal expansion % 1600°C | / | / | / | / | 1.8 | 1.8 | 1.8 | 1.6 |
Tips:
- SRMGe16/SRMGe18/SRMGe20/SRMGe22/SRMGe26=Fused Semi-rebond Magnesia Chrome Brick
- RMGe12/RMG14=Fused Rebonded Magnesia Chrome Brick
Model | SRMGe16 | SRMGe18 | SRMGe20 | SRMGe22 | SRMGe26 | RMGe12 | RMGe14 |
MgO % | 68 | 64 | 65 | 56 | 56 | 75 | 75 |
Cr2O3 % | 16 | 18 | 20 | 22 | 26 | 12 | 14 |
SiO2 % | 1.5 | 1.5 | 1 | 2.5 | 2.5 | 1.5 | 1.5 |
Apparent Porosity % | 16 | 16 | 14 | 16 | 16 | 15 | 15 |
Bulk Density g/cm3 | 3.1 | 3.1 | 3.1 | 3.1 | 3.1 | 3.2 | 3.2 |
Cold Crushing Strength Mpa | 40 | 40 | 40 | 40 | 40 | 50 | 50 |
Refractoriness Under Load °C | 1700 | 1700 | 1700 | 1700 | 1700 | 1700 | 1700 |